Things You'll Need
Serger needle
Small, flat-head screwdriver
Can of compressed air
Sewing machine cleaning brush
Dental floss
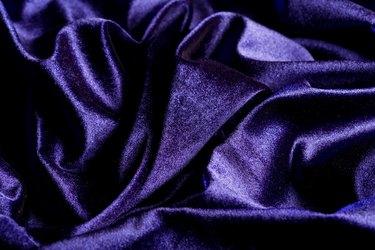
Before sergers leave the manufacturing facility, the timing is professionally set by technicians. Over time, a serger can lose its timing, causing the needle to skip stitches, break and possibly bump other parts of the machine. Thick fabrics, needle jams and thread debris can also cause a serger to have timing issues. Adjusting the timing of your serger can be done at home or by a professional at your local shop. Some sewers choose to adjust the timing themselves and save the $100 repair fee.
Step 1
Check the depth of the needle. If the needle is too high or too low, it will affect the timing of the stitches. Remove the bobbin case covering. Most models simply slide off, but some will need a small screwdriver. Install a new needle. Turn the wheel counterclockwise to lower the needle into its lowest position. View the needle from the front of the machine by the hook assembly, the entire eye of the needle should be visible. Adjust the needle bar with a small, flat-head screwdriver until you see the entire eye in the assembly. Tighten the screw when the needle bar is in the correct position.
Video of the Day
Step 2
Turn the wheel clockwise slowly and observe the needle as it rises up. The rotating hook assembly should pass the notch in the back of the needle at its midpoint as the needle moves upward. If the two parts are passing at another point, adjust the three large screws on the back of the hook. These screws attach the hook to the rotating shaft. Loosen the screws and twist the hook on the shaft while keeping the wheel stationary. Check the hook's rotation by lifting the needle with the wheel. When the needle and the hook pass each other at the appropriate spot, tighten the screws.
Step 3
Blow out any fabric or thread debris with a can of compressed air. Brush away any remaining dust with a small sewing machine cleaning brush. Replace the bobbin cover.
Step 4
Remove the looper cover. Run a piece of dental floss through the looper dials as if you were feeding thread through. Blow any remaining debris out with the can of compressed air. Replace the looper cover.
Video of the Day